Materials
-Customized material 632:Better than FS136, with higher nickel and chromium contents.
-Toughness, rust resistance, brightness effects are increased significantly.
-Mould base is made of stainless steel or P20(Preharden)with HRC 38~40.
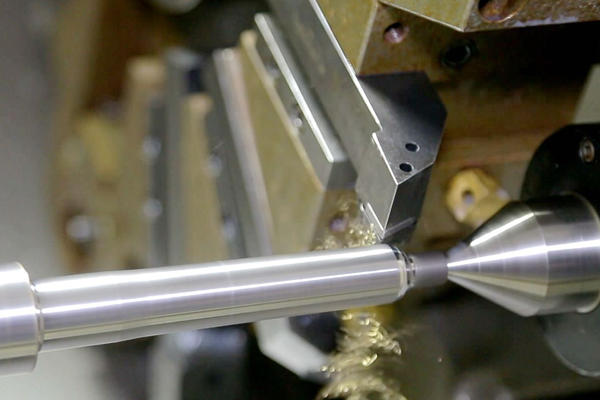
PET Preform Mould Specification | |
Mould name | 72 cavity preform mould for 30/25 Neck 11.5g Preform |
Mould cavity | 72 cavity |
Neck finish | 30/25 Neck finish |
Preform weight | 11.5g |
Insert materials | ASSAB FS136/Purpose made 632 |
Mould plate | 4Cr13/P20(Preharden) |
Hot plate | H13(Preharden) |
Heating coil | Rotfil from Italy/Hotset from Germany |
Copper nozzle | Beryllium bronze From Italy |
Insulator | From USA DU PONT |
Suitable injection molding machines | Husky, Netstal PET line, PET Master, General PET injection molding machine |
Location: | China |
Business Type: | Manufacturer, Exporter |
Brands: | BAINA |
Certificate: | ISO9001;CE;WRAS;GSG;National Torch Program Certificate |
Terms of payment and delivery: | 30% down payment;70% before shipment/FOB CIF |
Minimum order quantity: | 1 set |
Price: | Consultation |
Packing details: | Wooden pallet |
Delivery time: | 1-4 months |
Payment method: | T/T L/C |
1.We are one of the most reliable companies in this domain offering PET Preform Mould with advanced mould design technology.
Multicavity: 1-8 cavity, 12 cavity, 16 cavity, 24 cavity, 32 cavity, 48 cavity, 56 cavity, 72 cavity and 96 cavity.
Neck finish:PCO, 1810,1881,30/25,29/25,38 ,ALASK, ROPP; Jar neck and others.
-Customized material 632:Better than FS136, with higher nickel and chromium contents.
-Toughness, rust resistance, brightness effects are increased significantly.
-Mould base is made of stainless steel or P20(Preharden)with HRC 38~40.
-Thread splits are locked in position by lock rings before mould closing to minimize wear of thread split tapers on the cavity side and core side for a long flash-less service life of parting-lines.
Fountain or spiral cooling structure is used in the core.
Spiral waterway is used to milled outside the cavity,improve cycle efficiency and reduce cleaning times.
Neck drilled cross cooling channel.
Each plate is individually designed with a circulation cooling channel.
Optimized cooling layout is used to ensures fast and efficient heat exchange between steel and water and support fast cycle times to save energy costs.
Weight variation across cavities is minimal.
Excellent concentricity between core and cavity for minimum wall thickness variation.
Good mould life due to perfect matching of components under load.
Short injection and hold times.
Resin is exposed to less stress during injection.
Special hot runners design reduces material stress and working pressures.
Highly rigid to withstand clamping forces without deformation.
Provides adequate support to stack components.
Extreme resistance to corrosion.
Long service life.
Reduction in spares inventory for a group of moulds.
Easy servicing.
Comprehensive training provided to customer’s technicians in mould and hot runner maintenance as well as PET processing,
Professionally competent company technicians for mould commissioning, and training at the customer’s factory,
Standard wear parts are kept in stock for immediate shipment .