Summary:Preform molds are typically made from materials that can withstand high temperatures and pressures while maintaining dim...
Preform molds are typically made from materials that can withstand high temperatures and pressures while maintaining dimensional accuracy. The specific choice of material depends on the manufacturing process and the requirements of the preform being produced. Here are some commonly used materials for preform molds:
Steel: Steel molds are widely used in preform molding due to their excellent durability, hardness, and resistance to wear and tear. Typically, stainless steel or tool steel, such as P20 or H13, is used. These materials can withstand high temperatures and pressures and provide good mold life.
Aluminum: Aluminum molds are less expensive than steel molds and are often used for low-volume production or prototyping. While aluminum has lower durability and hardness compared to steel, it still offers sufficient strength and can be cost-effective for certain applications.
Beryllium copper: Beryllium copper molds possess excellent thermal conductivity, high hardness, and good corrosion resistance. These properties make them suitable for high-speed injection molding processes where rapid heat transfer is required. Beryllium copper molds are often used for high-volume production.
Invar: Invar is a nickel-iron alloy known for its low coefficient of thermal expansion, which means it has minimal dimensional changes with temperature variations. It is commonly used in processes where precise dimensional stability is crucial, such as in the production of optical components.
Composite materials: Some preform molds are made from composite materials, such as epoxy or carbon fiber reinforced polymers. These materials offer advantages like lightweight, high strength-to-weight ratio, and excellent resistance to corrosion. Composite molds are commonly used for certain specialized applications or when weight reduction is a priority.
It's worth noting that the choice of material for preform molds depends on factors like production volume, desired mold life, cost considerations, and the specific requirements of the molding process. Manufacturers may also use coatings or surface treatments to enhance the mold's performance and prolong its lifespan.
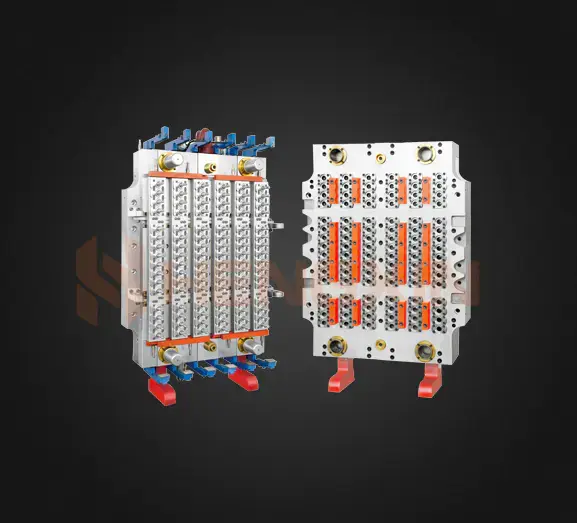