Summary:Designing a preform mold requires careful consideration of various factors to ensure efficient and successful production...
Designing a
preform mold requires careful consideration of various factors to ensure efficient and successful production. Here are some key factors that should be taken into account during the design process:
Preform shape and dimensions: The mold design should accommodate the specific shape, size, and dimensions of the preform required for the final product. Factors such as wall thickness, draft angles, and undercuts need to be considered to ensure proper mold filling, demolding, and dimensional accuracy.
Material selection: The choice of mold material should be based on factors such as the type of preform material, production volume, required mold life, and cost considerations. The selected material should have the necessary properties to withstand high temperatures, pressures, and wear while maintaining dimensional stability.
Mold flow analysis: Conducting mold flow analysis using specialized software can help optimize the mold design. This analysis simulates the injection molding process, providing insights into material flow, cooling rates, air traps, and potential defects. It helps identify areas of concern and enables adjustments to be made to improve part quality and cycle time.
Cooling system: Efficient cooling is crucial for maintaining cycle times and achieving consistent part quality. The mold design should incorporate an effective cooling system with appropriate cooling channels to ensure uniform cooling throughout the mold cavity. Properly designed cooling channels can help minimize warpage, reduce cycle times, and enhance productivity.
Venting and air evacuation: Adequate venting is necessary to allow air and gases to escape during the injection process, preventing part defects such as voids and burns. The mold design should include appropriate venting channels or venting inserts at suitable locations to facilitate efficient air evacuation.
Part ejection: The mold design should incorporate features such as ejector pins, lifters, or slides to enable easy and reliable part ejection from the mold. Proper consideration should be given to draft angles, part geometry, and demolding forces to prevent part damage or sticking.
Parting line and gate design: The location and design of the parting line (the line where the mold splits) and the gate (the point of injection) should be carefully determined. The parting line should align with the part's functional requirements, and the gate should allow proper filling and minimize gate vestige or other defects.
Mold maintenance and repair: The mold design should facilitate ease of maintenance and repair. Considerations should be made for accessibility to critical components, such as ejector pins, cooling channels, and hot runners, to allow for proper cleaning, maintenance, and potential repairs.
By considering these factors and collaborating closely with mold designers, manufacturers can optimize the preform mold design to meet their specific requirements and achieve efficient and high-quality production of preforms.
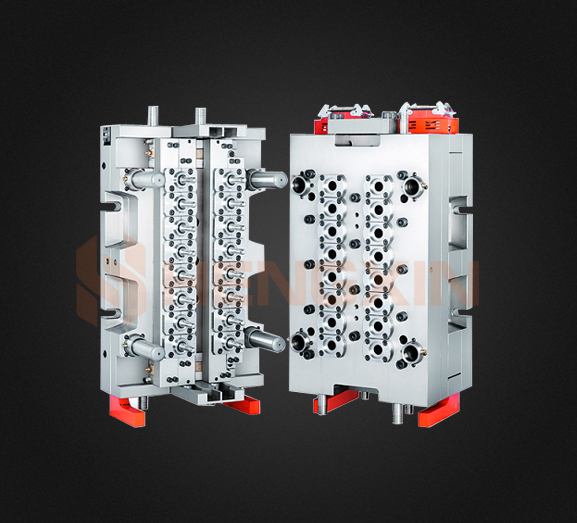