Summary:
Blow moulding is a process whereby a preheated, softened polymer is injected into a blow mould, which then inflates it ...
Blow moulding is a process whereby a preheated, softened polymer is injected into a blow mould, which then inflates it into the shape of a bottle or jar.
Jam can turn mouldy when it's stored over a long period or in the wrong conditions, and is exposed to mould spores in the air. It's important to prevent this from happening.
The extrusion blow moulding process is used to produce hollow plastic products, such as bottles and jars. It is faster than some other types of blow molding, allowing manufacturing companies to create hollow objects and parts more quickly than they could with other processes.
It is also a more cost-effective way to create these products. This method uses a tube-like mold known as a parison that contains molten plastic.
Once the heated plastic has melted, it's extruded into a parison and then blown with air to expand it. This is similar to glassblowing, which is also a type of blow molding.
Another advantage of this process is that it can be used to manufacture products with a consistent cross-section. This is especially helpful in the manufacturing of decorative trims, as well as those that mix various plastic attributes, such as hard and soft surfaces.
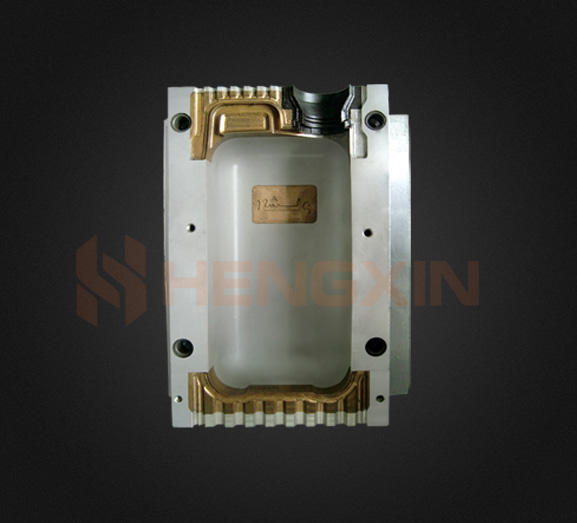
Injection Blow Molding
Injection blow moulding is a plastic forming process that involves the injection of molten polymer into a hollow, heated preform mold. This process can be used to create jars and bottles in various materials including PP, HDPE, PS, MIPS, and SAN.
This type of blow mould has a number of benefits, including reduced scrap material, fewer secondary trimming operations, and less energy usage. It also produces a high-quality, finished product that can be easily sold to consumers.
Compared with extrusion, injection blow molding is much more durable and can withstand higher temperatures. It is also more efficient because it requires a shorter cycle time.
This method can be adapted to make different shapes and sizes, as well as to meet a variety of manufacturing needs. It can be used to produce a wide range of products, including bottles for detergents, bleach, household cleaners, and food containers. It is also very easy to automate and reduce labor costs.
Hot Melt Blow Molding
Blow moulding is a plastic forming process that creates hollow containers. It can be used to make bottles, jars and other containers.
In the blow moulding process, plastic polymers are melted and then formed into a hollow tube called a parison. The tube is then clamped between molds and inflated with hot pressurized air.
Another type of blow moulding is called injection blow moulding, which consists of an extruder barrel and screw assembly that melts the polymer. It is then injected through nozzles into a heated mold cavity and core pin.
In this process, the molten polymer is poured into a preform, which consists of a bottle neck with a thick tube of plastic attached to it. The preform is then shaped into the final product and cured. This is an excellent method for a wide range of products, including pharmaceutical, personal care and motor oil bottles. It also allows for the use of orientated polypropylene, which has good impact resistance and moisture barrier properties.
Cold Melt Blow Molding
Blow moulding is one of the most popular methods used to manufacture hollow plastic products such as bottles and containers. It has a number of benefits including low tool and die costs, fast production rates and the ability to mold complex parts.
Cold melt blow moulding is another form of the process that utilizes air to shape molten plastic into a bottle, container or part. This method is used to make a variety of liquid bottles and containers such as water, juice and milk.
In this type of process the melted polymer is extruded into a tube known as a parison that’s placed in two halves of the mold. The air is then blown into the parison, inflating it into the hollow part based on the shape of the mold.