Summary:A blow mould for shaping bottle uses air pressure to produce a bottle. This process produces a parison, which is a verti...
A blow mould for shaping bottle uses air pressure to produce a bottle. This process produces a parison, which is a vertical tube made from plastic that allows compressed air to pass through it. The mold is made up of two parts, and the parison is inserted into the neck section. The blow pin is inserted into the neck of the bottle. The air pressure causes the parison to conform to the shape of the mould and the threads in the neck portion.
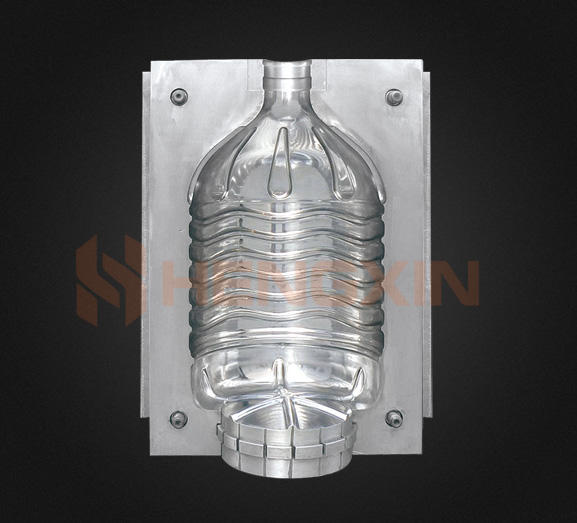
A blow mould for shaping bottle is made of a special material that is extruded. This material is used in many types of plastics and is mainly used for bottles. It is also used to produce high-quality miniature packaging. There are two types of blow moulds. The first type is made of plastic and the second one is made of glass. PET is the most commonly used material for making bottles. A Blow Mold for Shaping Bottle is a simple plastic bottle that is easy to form.
The next type of blow mould is made of a plastic material. It is used to produce bottles for the food and beverage industry. The process starts with the downward extrusion of a tube. Once it reaches a desired length, it closes and a blow-pin is inserted into the neck of the tube. The hot tube is then inflated inside the mould cavity. Once the plastic material cools, the blow mould opens and the bottles emerge from the mould.
Another type of blow mould uses plastic and uses a blow-pin to create the shape. The blow-pin is inserted into the neck end of the tube. The blow-pin forces the tube to fill the mould cavity. The process is repeated until the glass product is completely hard. Once this process has completed, the blow mould opens. The result is a perfectly shaped bottle. In addition to this, the mold is also extremely durable, which makes it a good choice for high-end bottle production.
Injection blow-moulding is another common technique used for shaping bottles. This technique requires a hot-wire tube that is heated above its glass transition temperature. The hot tube is then blown into a metal blow mould, using a core rod that stretches the tube to fill the mould cavity. This process is called stretch blow moulding. It is an excellent choice for making high-quality bottles. It is also economical.
A blow mould for bottle manufacturing is a simple process that uses a blow-pin to insert heated plastic into a metal blow mould. The process begins with a downward extrusion of a tube. The tube is cooled, and a blow-pin is inserted into the neck end. After the neck is shaped, the blown tube is inflated to fill the mold cavity. It is then cooled again before being released from the mould.
The blow-pin used in extrusion blow moulding is an important part of the process. The blow-pin is used to insert the tube into the mould cavity. After inserting the blow-pin, the tube is blown into the mould cavity. This process is called 'injection blow-moulding'. This method is used for small-sized bottles with tight tolerances in the neck. It is the most efficient and cost-effective way to make a bottle.
A blow mould is used to shape a bottle. The process begins by inserting a hot tube into a mold. The hot tube then closes and the blow-pin inflates the tube into the mould cavity. The finished blow-mould is then cooled and the final product is the desired shape. Then, the mold is removed and the bottle is ready to be shaped. The process is called extrusion blow moulding.
The extrusion blow moulding process involves the use of a long screw to extrude a tube. After it is extruded, it is shaped and captured in a mould. This process produces a variety of plastic bottles. Typically, these bottles are made from high-density plastic and are designed to hold liquids. Injection blow molding is used for large-scale manufacturing of plastic bottles.