Summary:
Blow molding is a process used to create plastic bottles, oil cans, and other containers. It can be done in a number of...
Blow molding is a process used to create plastic bottles, oil cans, and other containers. It can be done in a number of ways, depending on the bottle product you want to make and your available machinery.
PET is one of the most common plastics used in blow molding. It has many desirable characteristics, including easy processability, good clarity, water barrier properties and high resistance to odors and chemicals.
Reheating and Blow Molding
Blow molding is a plastic forming process that involves melting and inflating a tube-like structure known as a parison. It is usually formed from polyethylene or a similar material.
Food packaging - Thick liquids like milk, yogurt, mayonnaise, and ketchup require multi-layer packages to preserve the product. They can also be sprayed with acid resistant coatings to extend shelf life.
Marine products - Reservoirs, buoys, and other items for the water are commonly made with blow molding. They can be customized to fit a specific application.
Lawn and garden products - This industry uses blow molded plastic for mowers, power equipment fuel tanks, and oil storage and distribution. It is a good choice for this type of work because it can be made from a wide range of materials.
The two-stage reheat stretch blow molding (RSBM) process is a common manufacturing procedure for PET bottles. In this procedure, preform articles are injected and cooled in the first stage of production before they are stretch blow molded to form containers in the second stage.
Injection Stretch Blow Molding (ISBM)
Blow molding is an incredibly versatile manufacturing process that can be used for a wide variety of products. It's known for creating hollow plastic parts and features a number of benefits over other forms of plastic forming.
In a blow molding process, a hollow preform is heated and inflated by air. It then cools and hardens into its final form.
The most popular type of blow molding is injection stretch blow molding (ISBM). This is an ideal technique for thin, lightweight PET containers like single-serving water bottles and 2-liter carbonated soda bottles.
ISBM combines the strength and durability of injection molding with the flexibility of stretch blow. This produces crystal clear, lightweight PET bottles that are stronger and lighter than glass containers manufactured with other methods.
Injection Blow Molding (IBM)
Injection blow molding (IBM) is used to make hollow plastic objects in large quantities. It involves the injection molded polymer being injected onto a core pin; then it is rotated to a blow molding station to be inflated and cooled.
The process of blow molding is similar to that of extrusion but with more rigidity and durability in the end product. During the blowing stage, some stretch is added to the plastic resins, allowing them to be molded into strong containers.
This method of plastic manufacturing is more commonly utilized in the production of bottles and jars. Its advantages include a higher visual quality, greater durability and superior dimensional stability.
PET, HDPE and LDPE are the most common resins for this application. The plastics are inserted into the machine via preforms or parisons that are made in-house or purchased from suppliers.
Extrusion Blow Molding
Extrusion Blow Molding is the most common method of creating hollow plastic bottles, canisters or parts. It’s quicker than other blow molding processes and can produce larger parts than injection blow molding.
In this process, raw molten plastic is extruded into a tube-like mold called a parison. The parison is then inflated with air, which helps the molten plastic spread out against the walls of the parison to form a container or part.
After the parison reaches its desired length, two halves of a mold close around it. The mating surfaces on the mold pinch together the open areas of the tube and compressed air from a blown pin expands the parison to conform against the cold mold cavity walls.
The extruded plastic is then cooled and shaped. This process produces a variety of products, including small water bottles, lotion and other small containers, automotive parts and coolers. It’s also a good choice for making long cross-section shapes, such as windscreen wiper blades and vinyl signs and sidings.
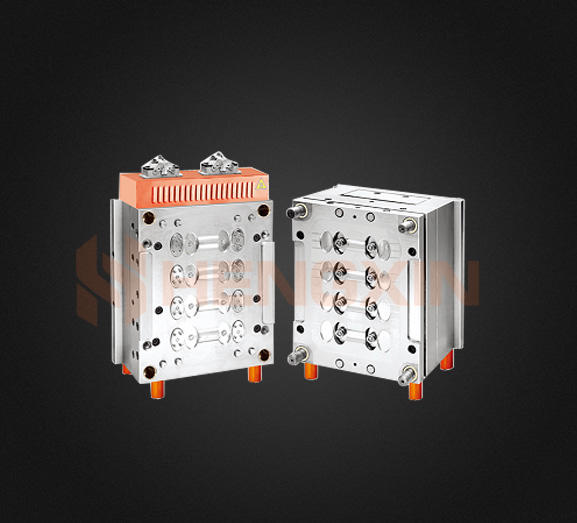